Hyundai Ioniq: High Voltage Battery System / Sub Battery Pack Assembly (Sub-BPA). Repair procedures
Check the target charging voltage when replacing with a new module |
Fault Code
1. | Turn OFF the ignition switch. |
2. | Connect the diagnostic tool device to the self-diagnosis connector (DLC). |
3. | Turn ON the ignition switch. |
4. | Check the "Fault Code" in the diagnostic tool fault diagnosis. |
5. | When the following fault code is identified, check the faulty module and replace the cell monitoring unit or the corresponding module. –
| Fault of voltage sensing area/overvoltage/ low voltage/ voltage deviation of the high voltage battery. |
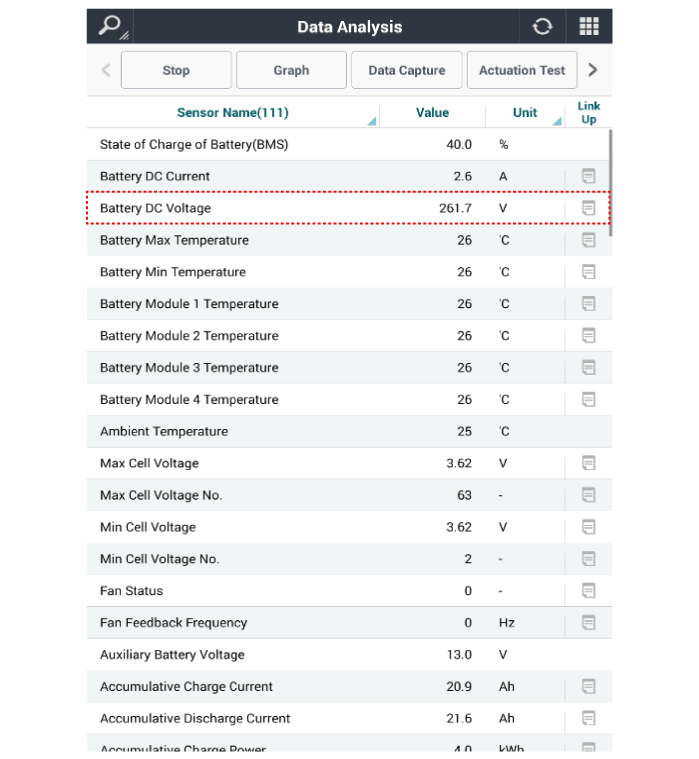
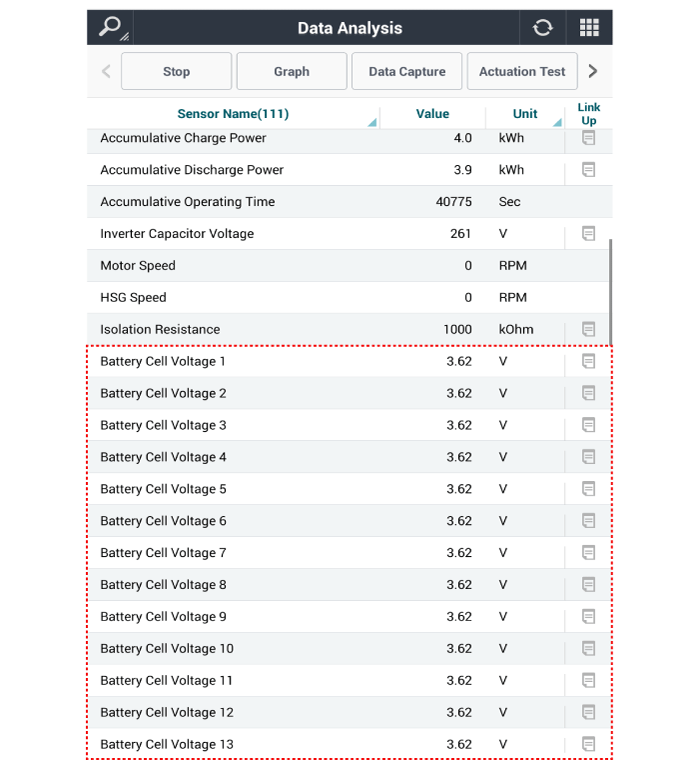
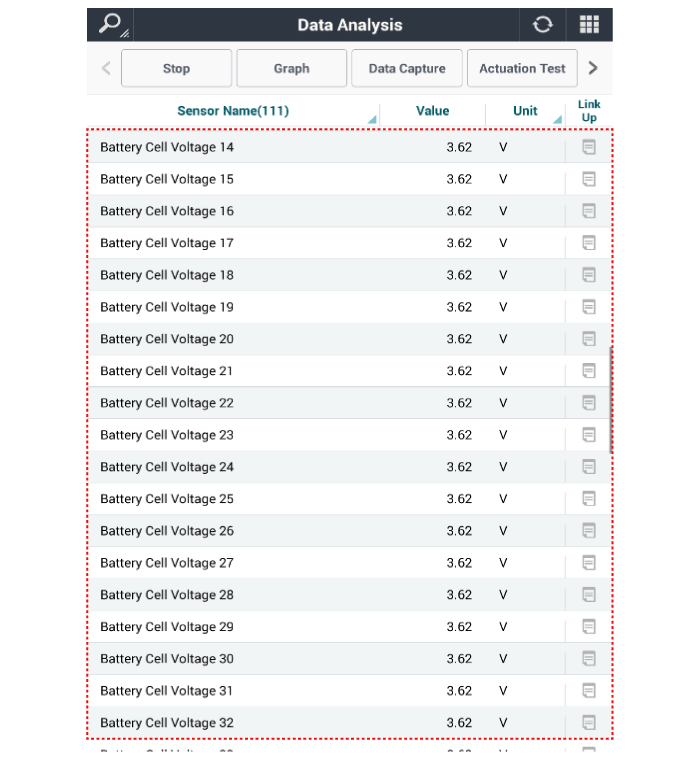
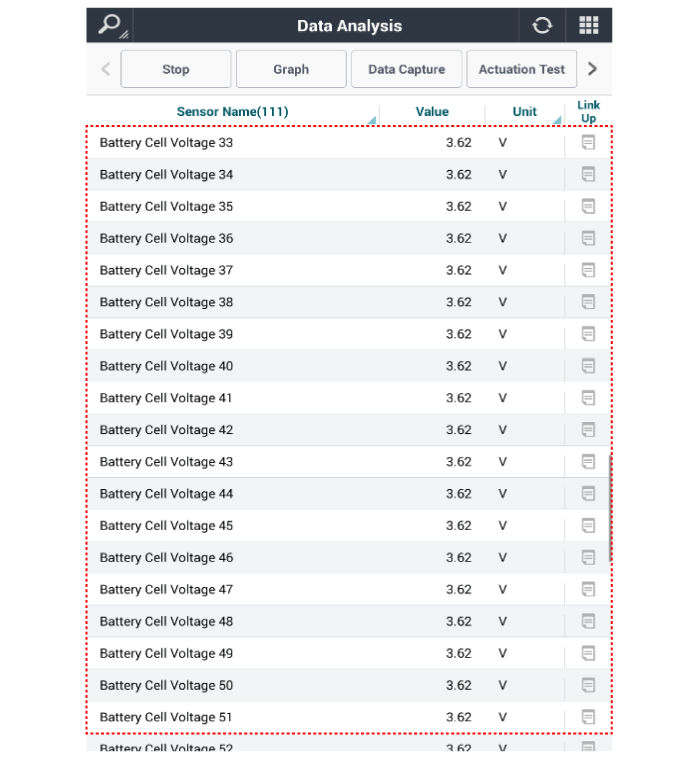
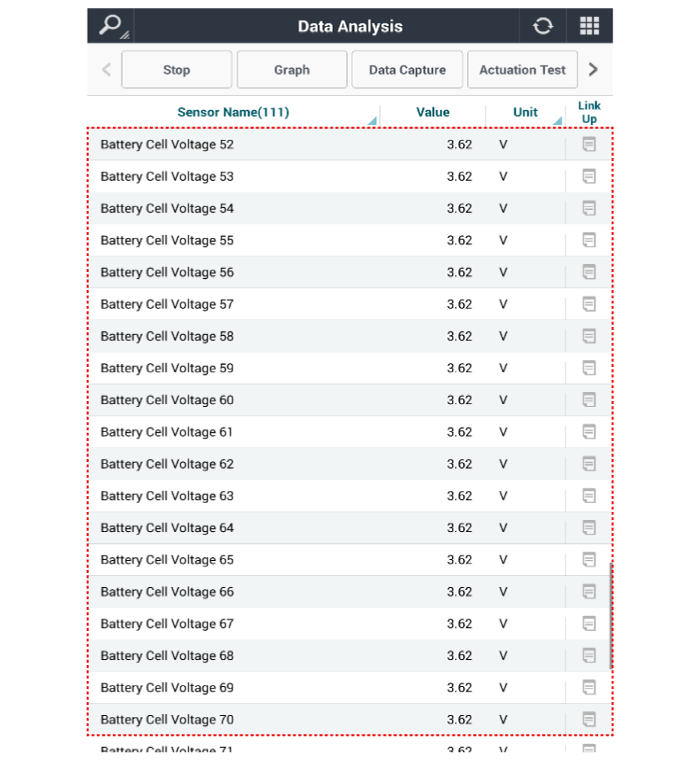
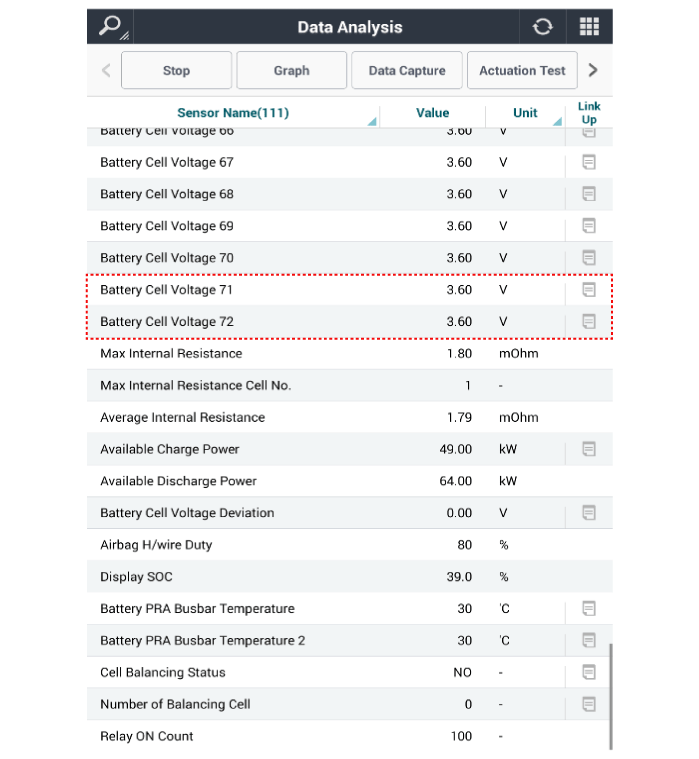
(1) | If the temperature of the battery module is normal see the "cell voltage" of the diagnostic tool service data and check the faulty cell’s number. Cell Voltage : 2.5V - 4.3V |
|
(2) | Refer to the table below and check the module number that includes the faulty cell identified during the no. •
| If the faulty cell’s number is 10, the module number is 1. |
|
Cell No
| Cell Module NO
| 01 - 16
| Battery Module #1
| 17 - 32
| Battery Module #2
| 33 - 48
| Battery Module #3
| 49 - 64
| Battery Module #4
|
|
|
Cell balancing tool available
1. | Turn OFF the ignition switch. |
2. | Connect the diagnostic tool device to the self-diagnosis connector (DLC). |
3. | Turn ON the ignition switch. |
4. | Check the maximum and minimum voltages of the cell included in the normal module (excluding the cell numbers identified during the no. 1 process) through the "cell voltage" of diagnostic tool service data. •
| If the cell number of the module including the faulty cell is 09 - 16, check the maximum and minimum voltages of 1 - 8 and 17 - 72 cells. |
|
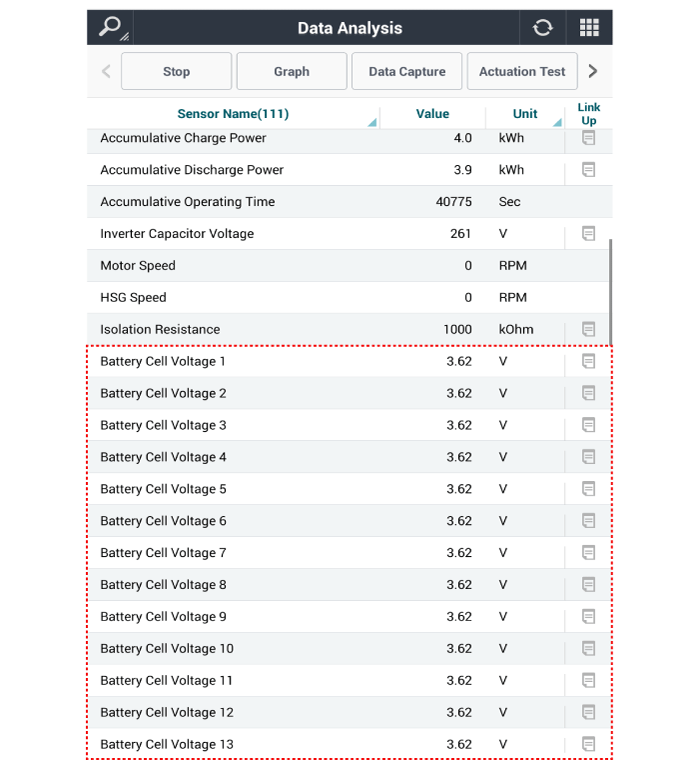
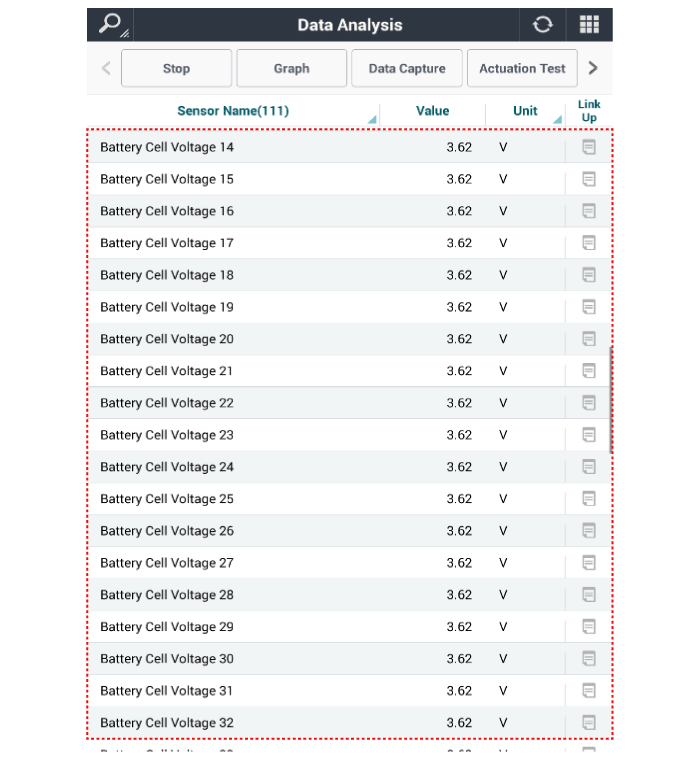
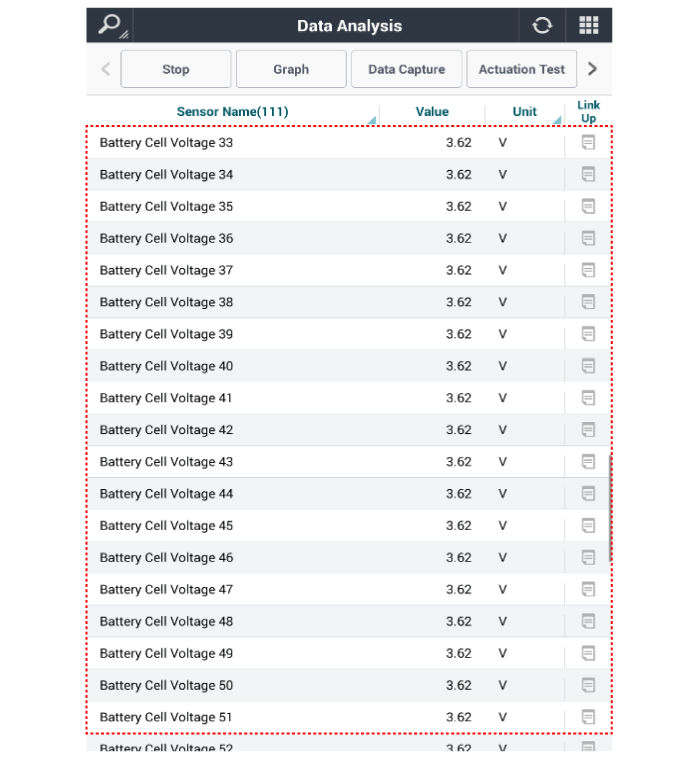
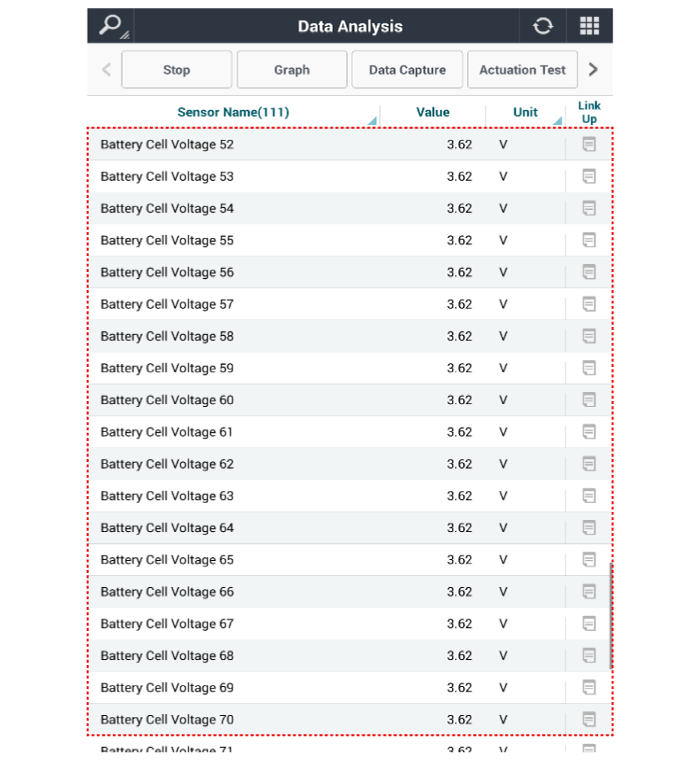
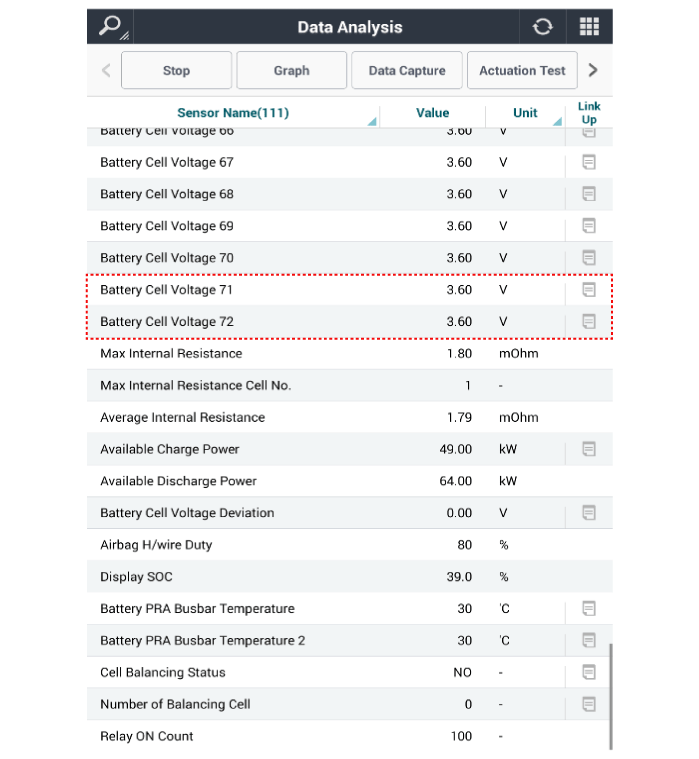
|
5. | Put the maximum voltage and minimum voltage identified during the no. 4 process to the below formula and calculate the target charging voltage when replacing with the new module. |
6. | Before installing the new module, charge or discharge the new module to the target voltage using MIDTRONICS (xMB-9640 Module Balancer). Target charging voltage : (Max. voltage + Min. voltage) / 2 * number of the cells of the new module |
※ It is necessary to calculate the minimum/maximum cell voltage from the cells of the normal modules except the faulty modules. 
1) | Exclude the No.1 module including the No.20 cell with bad voltage from calculation as it should be replaced with a new one. |
2) | Check the minimum/maximum cell voltage of the No. 2 - 5 modules in the service data except the No.1 module. |
3) | Calculate the target charging voltage with reference to the minimum/maximum cell voltage identified in step 2. • Target charging voltage = (maximum cell voltage + minimum cell voltage) / 2 * the number of cells of new module • 23.46V = (3.92 V + 3.9 V) / 2 * 6cell |
4) | Install the new module after charging or discharging it with reference to the target charging voltage obtained in step 3. |
|
|
Cell balancing tool not available
•
| Refer to the below procedure to perform cell balancing. 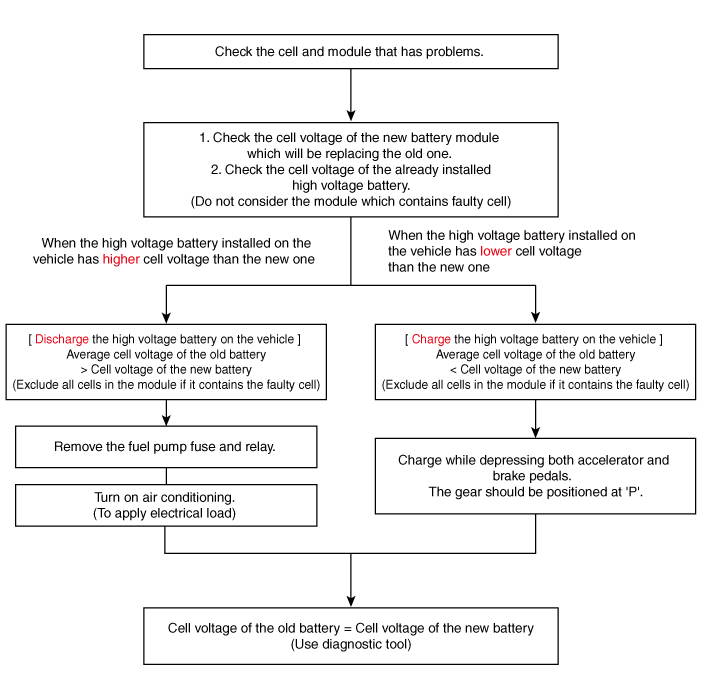
|
|
1. | Locate the module containing the cell with problem, using diagnostic tool. (Sensor data diagnosis → Battery Management System (BMS) → Battery pack voltage, maximum cell voltage, minimum cell voltage) |
2. | Check the voltage of all cells except the module which does not contain the cell with issues. |
3. | Check the voltage of the new module. Then calculate the average voltage by dividing the module voltage by the number of the cells. 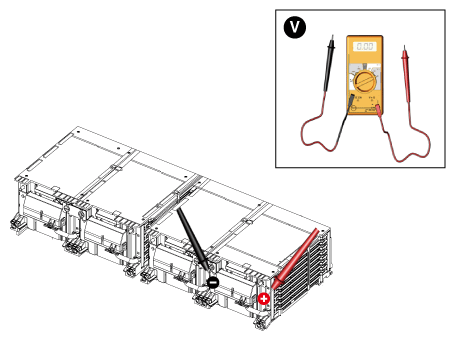
|
1. | Discharge the cell while cheking the voltage using diagnostic tool. (Sensor data diagnosis → Battery Management System (BMS) → Battery pack voltage, maximum cell voltage, minimum cell voltage) |
2. | Remove the engine room junction box. |
3. | Remove the fuel pump fuse (A). 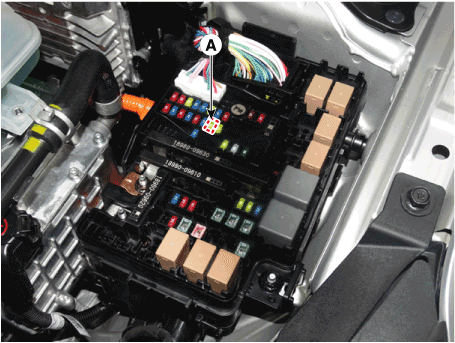
•
| Parts to be removed vary from vehicle to vehicle, depending on the specification. ① 2 fuel pump fuses ② 1 fuel pump fuse ③ 1 fuel pump fuse and 1 engine power relay |
|
|
4. | Turn on the air conditioning to discharge high voltage battery. (To overload the electrical system) Continue until the voltage of the battery matches the voltage of the new module cell. •
| The plus and minus signs on the diagnostic tool screen refers to the charge and discharge. ( + ) : Charge ( - ) : Discharge |
|
•
| If the voltage of the faulty cell reaches 2.8V while discharging, 'the maximum dischargable power' becomes 0kW and additional discharge is disabled. In such case, repeat pressing IG on/off to discharge the voltage until it meets the target. |
•
| The voltage of the battery packs may be vary depnding on the air conditioning and other electrical load condition. However, the recommended voltage is between 5 - 10 A. |
|
|
1. | Charge the cell while cheking the voltage using diagnostic tool. (Sensor data diagnosis → Battery Management System (BMS) → Battery pack voltage, maximum cell voltage, minimum cell voltage) |
2. | Depress the accelerator and brake pedals at the same time for charging. (To run the engine) •
| Charging condition : IG on, gear at P, air conditioning load off |
|
|
3. | Simultaneously depressing the both pedals will create the pack voltage approximately -20A. At the moment the voltage reaches the target, immediately release the pedals. It will temporarily drop the pack voltage to 0V, causing voltage dip approximately 40mV. Therefore charge about 40mV more than the target voltage. •
| The plus and minus signs on the diagnostic tool screen refers to the charge and discharge. ( + ) : Charge ( - ) : Discharge |
|
•
| If the voltage of the new module cell is 3.74V, charge up to 3.78V. ※ Once stop charging, cell voltage on the diagnostic tool drops about 0.04V and becomes 3.74V. |
|
|
•
| This hybrid system uses a DC 270V voltage system. Be sure to follow safety instructions below. Failure to follow safety instructions may result in serious injury or electrocution. (Refer to "Safety Precaution") |
|
1. | Remove the BMS ECU, power relay assembly, cooling fan extension wiring (A). |
2. | Remove the installation bolt, then remove the safety plug cable (B). 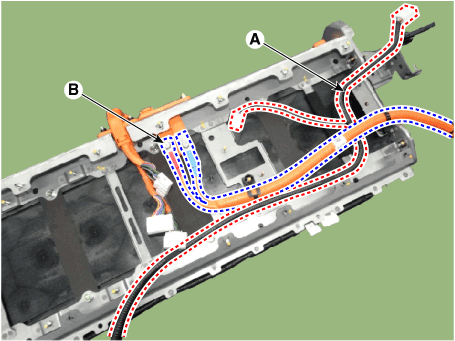
|
3. | Remove the installation nut, then remove the battery pack assembly front cover (A). 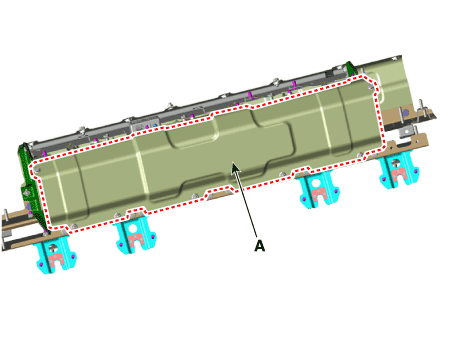
|
4. | Remove the installation nut, then remove the battery pack assembly rear cover (A). 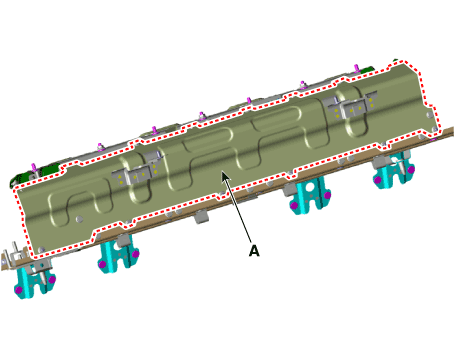
|
5. | Remove the battery temperature sensor (A). 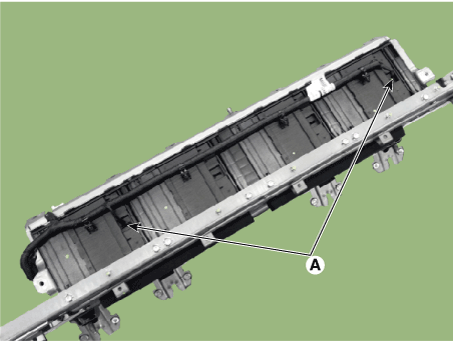
|
6. | Remove the installation nut, then remove the battery module connector (A). |
7. | Remove the installation nut, then remove the power cable (+) terminal (B) and (-) terminal (C) 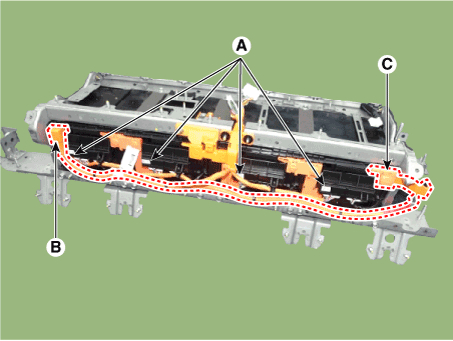
|
8. | Remove the installation nut, then remove the safety plug bus bar (A). 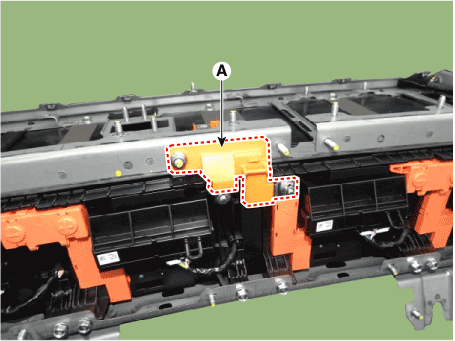
|
9. | Remove the installation bolt, then remove the battery pack bracket (A). 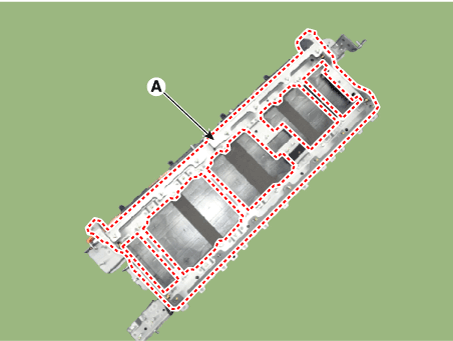
|
10. | Remove the installation bolt, then remove the battery module (A) from the high voltage battery plate. 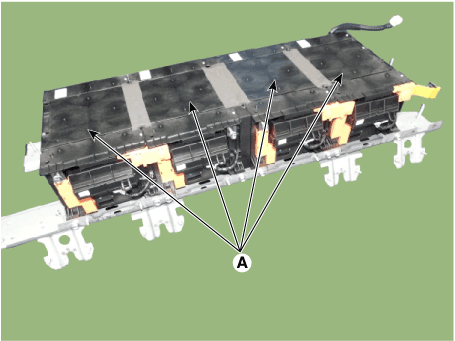
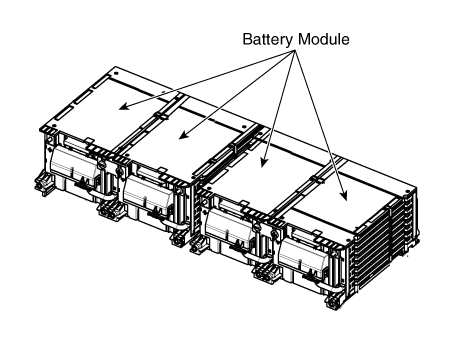
|
•
| This hybrid system uses a DC 270V voltage system. Be sure to follow safety instructions below. Failure to follow safety instructions may result in serious injury or electrocution. |
|
1. | Install the battery pack assembly in the reverse order of removal. Battery pack frame installation bolt & nut : 7.8 - 11.8 N.m (0.8 - 1.2 kgf.m, 5.8 - 8.7 lb-ft) Battery pack cover installation bolt : 7.8 - 11.8 N.m (0.8 - 1.2 kgf.m, 5.8 - 8.7 lb-ft) Power cable terminal tightening nut : 7.8 - 11.8 N.m (0.8 - 1.2 kgf.m, 5.8 - 8.7 lb-ft) Battery module installation bolt : 7.8 - 11.8 N.m (0.8 - 1.2 kgf.m, 5.8 - 8.7 lb-ft) |
|
Removal
•
Be sure to read and follow the "General Safety Information and Caution" before doing any work related with the high voltage system...
DescriptionThe Power Relay Assembly (PRA) consists of the positive and negative main relays, pre-charge relay, pre-charge resistor and battery current sensor...
Other information:
Operation and Leakage CheckCheck all of the following items : Component Procedure Integrated Brake Actuation Unit (IBAU) (A) and Pressure Source Unit (PSU) (B)Check brake operation by applying the brakes during a test drive...
Replacement1.Disconnect the negative (-) battery terminal. 2.Remove the heater and blower assembly.(Refer to Heater - "Heater Unit") 3.Loosen the mounting screws and remove the driver's temperature control actuator (A).4.Remove the heater core cover (A) after loosening the mounting screws...
Categories
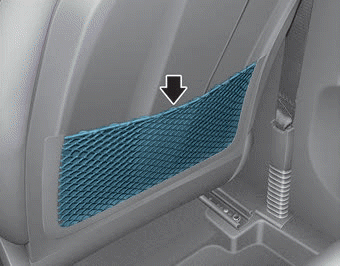
The seatback pocket is provided on the back of the front passenger's seatback.
WARNING
To prevent the Occupant Classification System from malfunctioning:
read more